Specific Selection Suggestions for PET Coated Tie Wire


The selection of PET coated tie wires should be combined with the performance requirements, environmental conditions and cost requirements in specific application scenarios. The following are specific selection recommendations and analysis:
1. Selection by application scenario
Electronic/Electrical Industry
Core requirements: high insulation, anti-static, high temperature resistance, and chemical corrosion resistance.
Selection recommendations:
Anti-static coating: suitable for bundling electronic components to avoid electrostatic damage.
High temperature resistant coating: For long-term use in high temperature environments (such as below 150°C), it is necessary to select a PET substrate with good temperature resistance (such as PET temperature resistance of 120°C-150°C).
Anti-corrosion coating: For use in chemical corrosion environments, acid and alkali resistant coating materials (such as polyurethane coatings) are required.
Agriculture/Aquaculture
Core requirements: weather resistance, UV resistance, high strength, and non-conductive.
Selection recommendations:
UV-resistant coating: To extend the outdoor service life, it is recommended to use PET plastic steel wire with added UV absorbers.
High-strength substrate: Select a PET substrate with high tensile strength (such as a tensile strength of 9 times that of HDPE film), which can withstand greater tension.
Non-conductive coating: avoid impact on greenhouse equipment or crops.
Industrial packaging/logistics
Core requirements: high strength, wear resistance, weather resistance, cost-effectiveness.
Selection suggestions:
High-strength PET coated tie wire: suitable for heavy cargo bundling, need to choose a thicker substrate (such as 50μm or more).
Wear-resistant coating: add wear-resistant nanoparticles (such as silica sol coating) to improve scratch resistance.
Economical products: Under the basic performance requirements, choose low-cost PET substrates and coating processes (such as roller coating).
Medical/food field
Core requirements: environmental protection and non-toxicity, antibacterial, chemical resistance.
Selection suggestions:
Medical-grade PET coated tie wire: meets RoHS, FDA and other standards, using halogen-free and heavy metal-free coating materials.
Antibacterial coating: suitable for medical equipment or food packaging, antibacterial agents such as silver ions can be added.
Chemical resistant coating: maintains stable performance when wiped with chemicals such as alcohol.
2. Selection by performance requirements
High strength requirements
Substrate selection: Choose a PET substrate with high tensile strength (such as a tensile strength that is 3 times that of PC and PA films).
Coating design: Use a multi-layer coating structure to enhance tensile strength and wear resistance.
Weather resistance requirements
UV-resistant coating: Add UV absorbers or stabilizers to extend outdoor service life.
Moisture-resistant coating: Suitable for high humidity environments to avoid hygroscopic expansion or deformation.
Environmental protection requirements
Halogen-free coating: Avoid the harm of halogens to the environment and human body.
Water-based coating: Reduce VOC emissions and comply with environmental regulations.
Functional requirements
Antistatic coating: Suitable for the electronics industry to avoid static electricity accumulation.
Antibacterial coating: Suitable for the medical or food industry to inhibit the growth of microorganisms.
3. Selection by environmental conditions
High temperature environment
Heat resistance requirements: Choose a PET substrate with good temperature resistance (such as short-term temperature resistance of 150°C) and match it with a high temperature resistant coating (such as silicone pressure-sensitive adhesive).
Chemical corrosion environment
Chemical resistant coating: Choose acid, alkali and solvent resistant coating materials (such as polyurethane coating).
Outdoor environment
UV resistant coating: Add UV absorber to extend service life.
Weather resistant coating: Improve anti-aging performance to avoid yellowing or embrittlement.
IV. Selection based on cost-effectiveness
Large-scale application
Economical PET substrate: Choose a lower-priced PET substrate to meet basic performance requirements.
Efficient coating process: Use processes such as roller coating and slope extrusion coating to improve production efficiency and reduce costs.
High-end application
High-performance PET substrate: Choose a high-strength and high-transparency PET substrate to meet high-end needs.
Functional coating: According to specific needs, add functional coatings such as antistatic and antibacterial to increase product added value.
Qingdao Chenan Machinery Co., Ltd. has the advantage of developing and producing rubber winding equipment, with higher technology than various equipment assembly manufacturers in the industry. For more information about PET coated tie wire, please contact us.
Company: Qingdao Chenan Machinery Co., Ltd.
Address: Yanjialing Industrial Park, East Chengma Road, Tongji New Economic Zone, Jimo District, Qingdao City, Shandong Province
Email: qdcajx@gmail.com
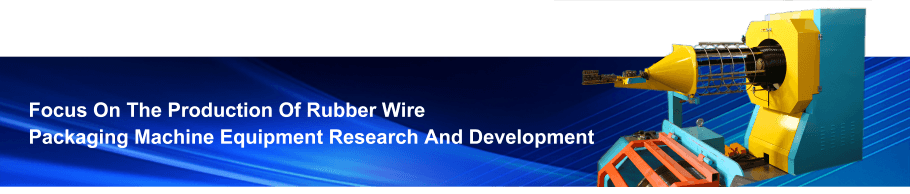
Recommended
08-28Core Characteristics of PET Coated Iron Wire
08-27Selection Criteria for Nylon Coated Wire Factories
08-21Core Characteristics of PET Coated Wire Mesh
08-20Core Properties of PVC Coated Nylon Wire
08-14Production Process of PET Coated Tie Wire
08-13Core Properties of Nylon Coated Stainless Steel Wire Rope